In the world of precision engineering and manufacturing, the performance and efficiency of machinery are crucial factors. Precision spindle assemblies play a vital role in various industries, including aerospace, automotive, electronics, and medical devices. These assemblies consist of numerous intricate parts that work together to ensure accurate and efficient rotational motion.
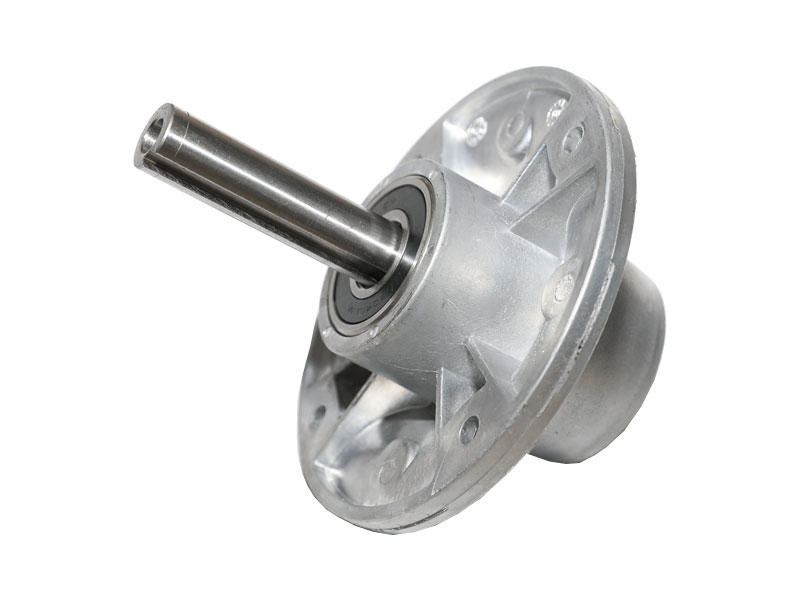
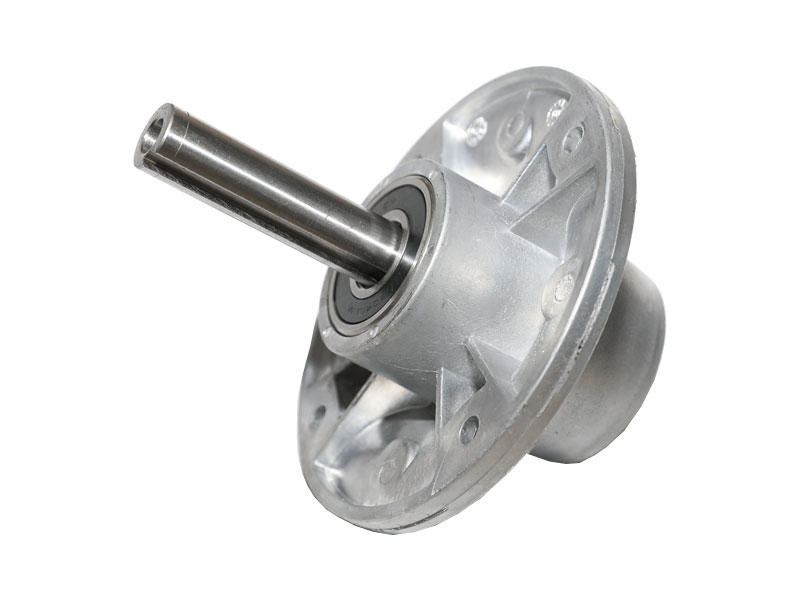
Spindle Shaft
The spindle shaft is the central component of a precision spindle assembly. It serves as the axis of rotation and transmits power to the cutting tool or workpiece. The shaft is manufactured with high-quality materials, such as hardened steel or ceramic, to ensure durability, rigidity, and resistance to deformation. Precision machining processes are employed to achieve precise dimensions and tolerances, minimizing any vibration or deflection during operation.
Bearings
Bearings are critical components that support the spindle shaft and facilitate smooth rotational movement. Precision spindle assemblies often utilize high-precision ball bearings or roller bearings. These bearings are designed to minimize friction, maximize stiffness, and provide high radial and axial load capacities. Advanced technologies, such as ceramic ball bearings or hybrid bearings, are employed to enhance performance by reducing heat generation and increasing operational speed.
Housing and Casing
The housing and casing of a precision spindle assembly provide structural support and protection for internal components. They are typically made from materials such as aluminum, cast iron, or stainless steel, depending on the specific application requirements. The housing ensures proper alignment of the spindle components, minimizes vibration, and helps dissipate heat generated during operation. It may also incorporate cooling mechanisms, such as liquid or air cooling, to maintain optimal operating temperatures.
Drive Mechanism
The drive mechanism is responsible for transmitting power to the spindle shaft. It can be a motor, belt drive, gear system, or a combination of these components. The choice of the drive mechanism depends on factors such as desired rotational speed, torque requirements, and the nature of the application. High-precision drive mechanisms are utilized to ensure accurate speed control and minimize backlash, resulting in precise positioning and improved surface finish.
Lubrication and Cooling Systems
Precision spindle assemblies often incorporate lubrication and cooling systems to ensure proper functioning and extend the lifespan of the components. Lubrication prevents wear, reduces friction, and dissipates heat generated during operation. Various lubrication methods, such as oil mist, grease, or air-oil lubrication, are employed based on the spindle's speed and load requirements. Cooling systems, such as coolant channels or temperature-controlled environments, help maintain stable operating temperatures and prevent thermal expansion that could affect precision.
Monitoring and Control Systems
To achieve optimal performance, Precision Spindle Assembly Parts may feature monitoring and control systems. These systems utilize sensors and feedback mechanisms to measure factors such as temperature, vibration, and speed. Real-time monitoring allows for early detection of potential issues, enabling preventive maintenance and reducing downtime. Advanced control systems can automatically adjust spindle speed, acceleration, and deceleration rates, optimizing performance for different machining tasks.
Precision spindle assembly parts play a vital role in ensuring the performance and efficiency of machinery in various industries. The careful selection and integration of high-quality components, such as the spindle shaft, bearings, housing, drive mechanism, lubrication, and cooling systems, contribute to accurate rotational motion, reduced vibration, and extended lifespan. Furthermore, monitoring and control systems enhance overall performance and enable proactive maintenance. By prioritizing the use of precision spindle assembly parts, manufacturers can achieve improved productivity, superior surface finishes, and enhanced precision in their machining operations.